This leaf-shaped lamp, I designed for the course Manufacturing & Design about production techniques in the bachelor Industrial Design Engineering. I chose the production technique “sand casting”, that I elaborately investigated including a visit of the aluminum factory MGP in Venlo. This post will show first my design of a stackable aluminum lamp, followed by my investigations of the production process.
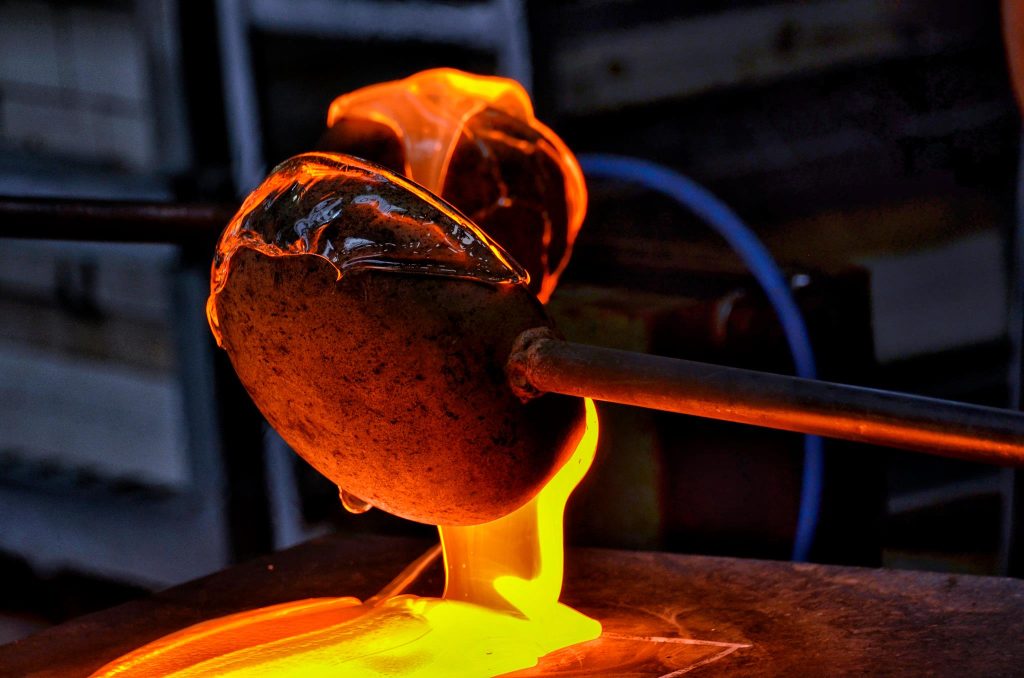
Aluminums most special properties are heat induction and light reflection. Based on nature, a lamp with a wide stem in a conical shape and a thin branch with large leaf, as a lamp, came into being. The leaf has a solar cell on top, that captures solar energy just like the leaf of a plant captures the sun and converts it into energy for the light to shine in the nighttime through a light-sensitive resistor. I created this model of this stackable, organically shaped lamp in SolidWorks.
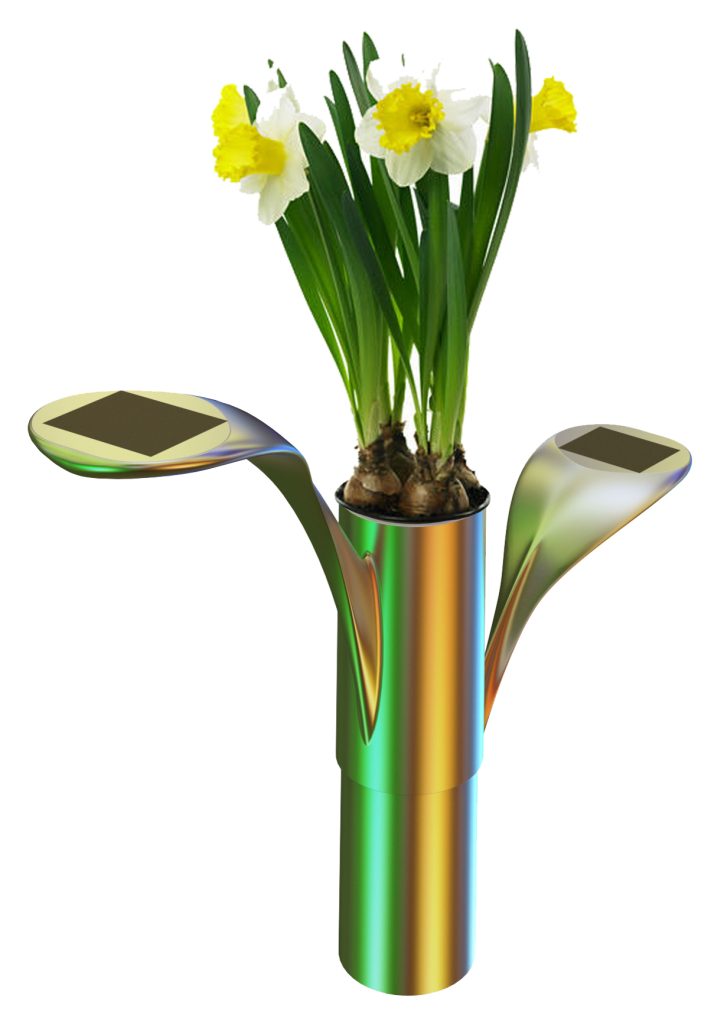
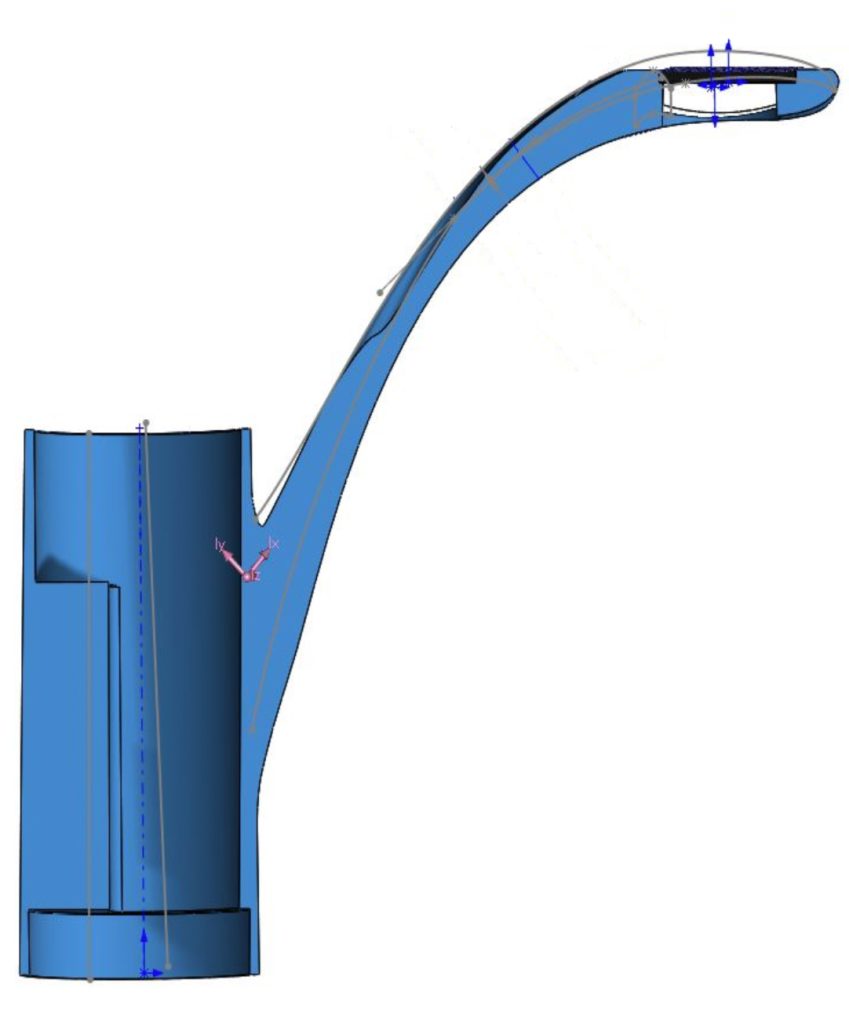
Extra weight is added to the opposite to the leaf side of the stem to prevent the lamp from tipping over. The center of gravity is shifted to the pink arrow, making it stable even when stacking. Using the top as plant holder creates extra stability.
Lamps can be stacked because of the conical shape in the stem. The bottom is wider and fits snugly over the top of itself, making two identical lamps fit together into one. At the bottom of the conical shape is a ledge that falls on the top of the lamp below, keeping the stack straight regardless of its height.
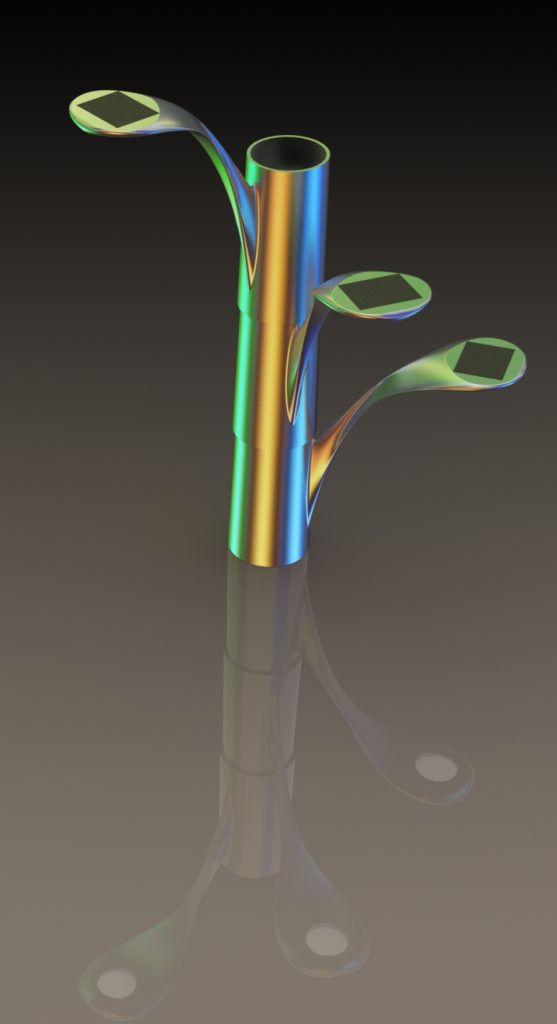
With sand casting, a mold can only be used once. The advantages are a freedom of alloy choice, complex shape possibilities and an absence of high investment in the permanent mold. This makes it a suitable production process for small runs. A disadvantage is the more limited freedom of shape than with mold casting and that sand casting is quite labour-intensive since the process is manual.

At MGP, the aluminum is manually poured into the mold. The speed at which you fill a mold is very important since the product does not have to be partially solidified. Ash pins, windows and filling places are used to regulate this. MGP only works with aluminum alloys. Due to this specialization, a lot of attention has been paid to optimization of production and heat treatments. In addition, aluminum is easy to recycle. The materials contained in the alloys and their properties are:
- Silicon: increases fluidity, but decreases heat crack resistance
- Magnesium: increases strength and hardness
- Copper: increases strength and hardness
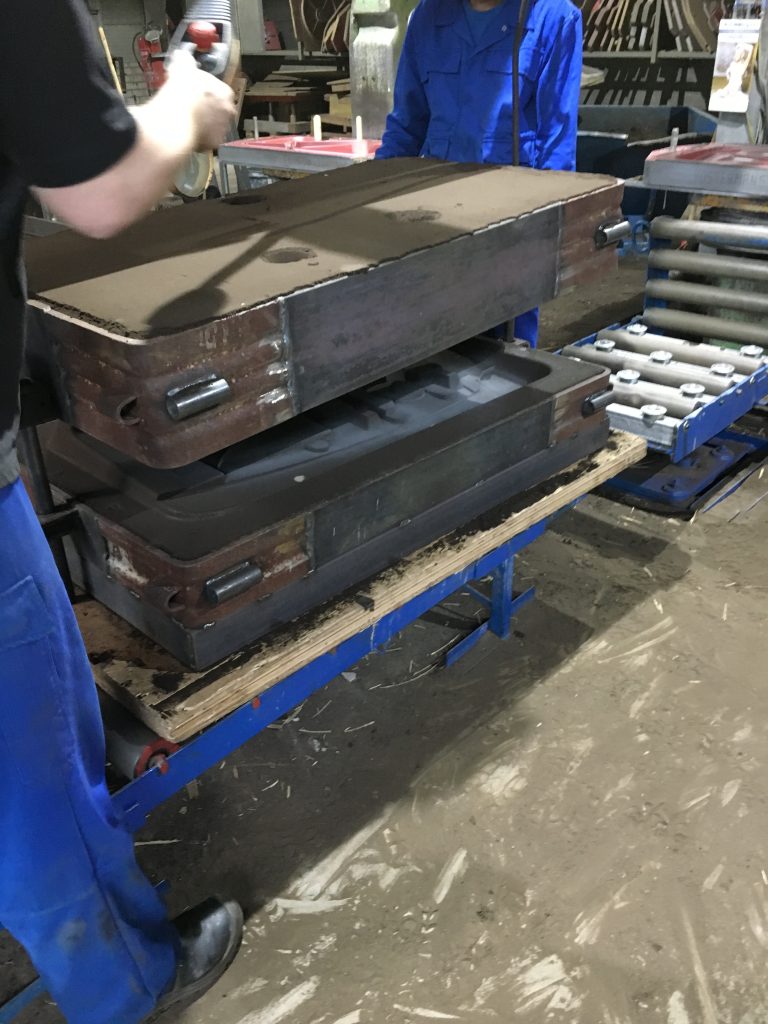
With this knowledge on the manufacturing process, a mold for the leaf lamp is drawn.
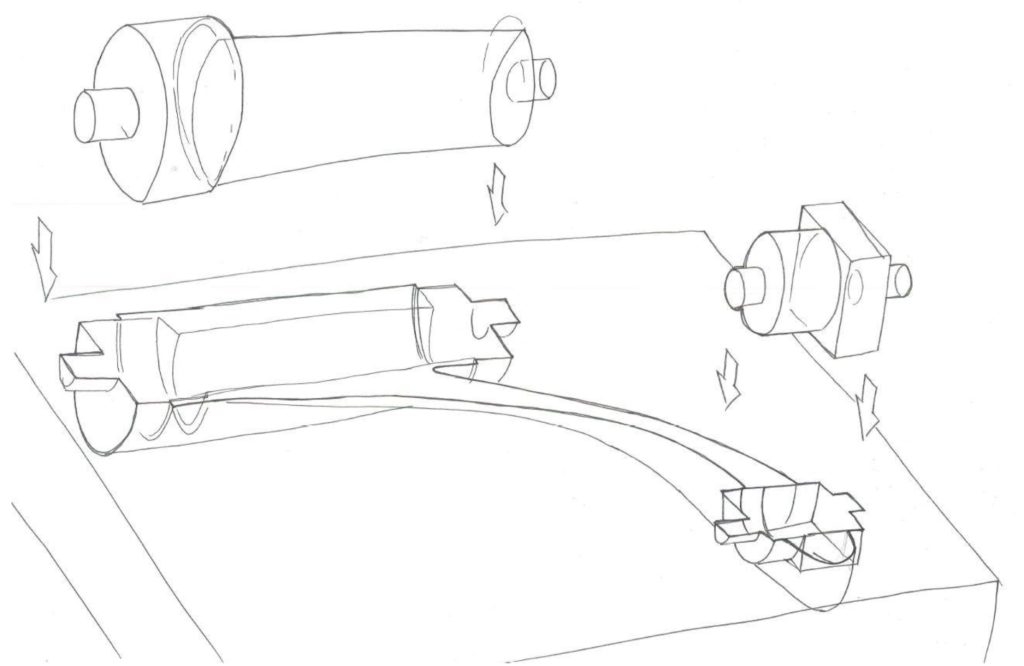